South Texas Operator Reduces Emissions and Sand Erosion Damages with Flowback 2.0
The Problem
An operator in South Texas was continuously dealing with emissions issues with the local EPA, as a result of the test separators and frac tanks required with their large footprint for traditional flowback operations. They needed to use two to three sand separators at a time because their sand management system was not an engineered fit-for-purpose solution. Even with test separators, they were still ending up with sand at the production facility.
They needed a solution that was going to reduce their equipment footprint, improve sand management, and minimize emissions at the same time.
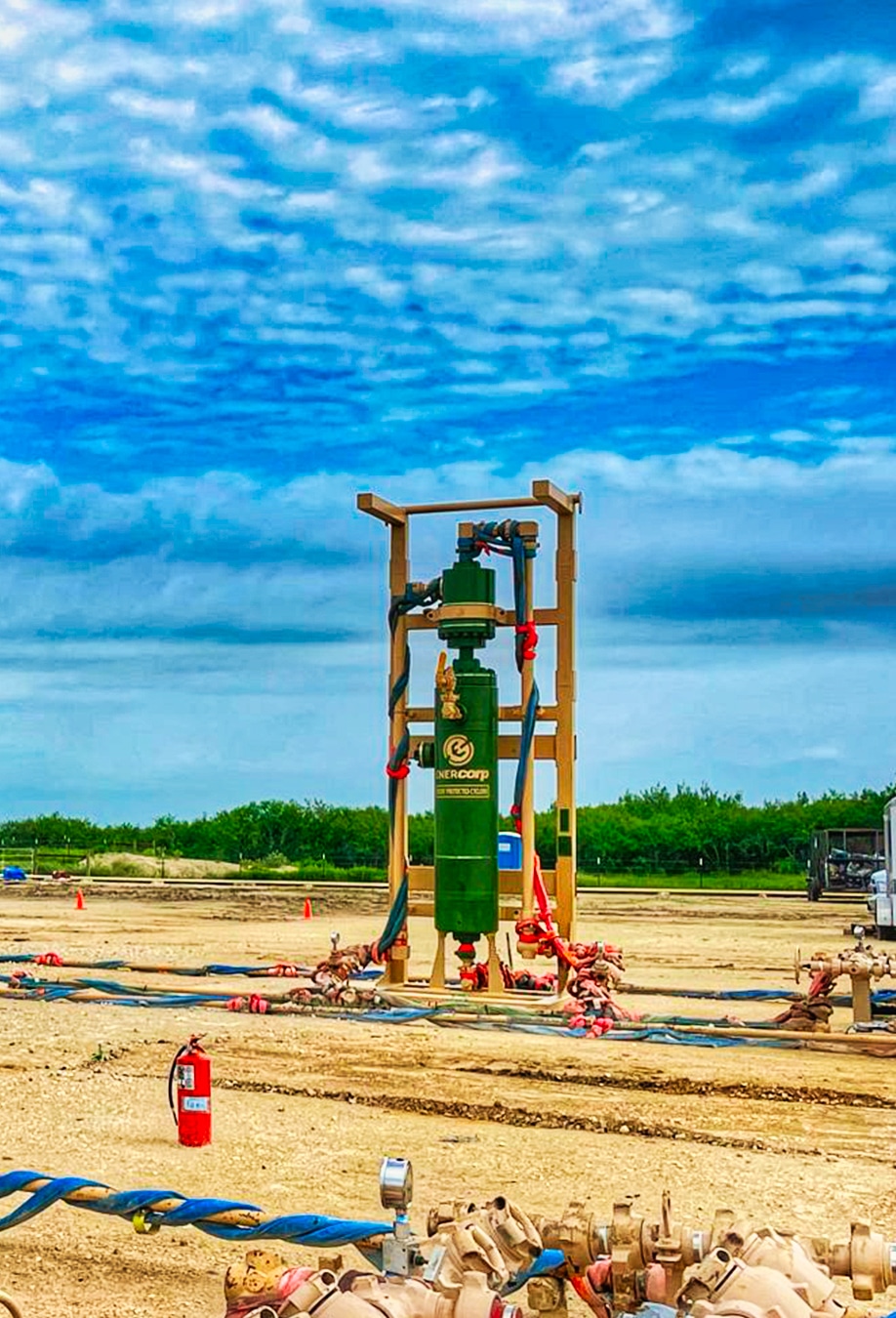
The Solution
Our team of engineers suggested the operator consider Flowback 2.0 with the Sahara Advanced Sand Cyclone. It would enable them to remove the test separators all together and eliminate any sand issues at their production facility.
Not only that, but the Sahara Advanced Sand Cyclone minimizes emissions by bypassing frac tanks entirely and flowing directly into the production facility. This greatly reduces the potential points of emissions and environmental hazards.
The Results
- Minimized equipment footprint: With no test separators or frac tanks required, the sand management program only utilizes one highly engineered sand separator.
- Increased sand capture: The Sahara Advanced Sand Cyclone captures 97% or more of sand, considerably reducing the chances of damages and costs related to sand erosion at the production facility.
- Lower labor costs: The operator was also able to reduce labor costs with Flowback 2.0, eliminating one person per shift per pad from day one of flowback.
- Environmentally sound system: They were able to tie in extra storage downstream of their production tanks to account for the higher volume of returns, creating a closed loop flowback system.
The operator was so pleased with the results, that they will continue to use the Flowback 2.0 setup moving forward.
Are you concerned about emissions at the wellsite or do you need to improve your sand capture rate and minimize sand erosion damages? Get in touch with EnerCorp today to learn about how we can help you reach your goals.
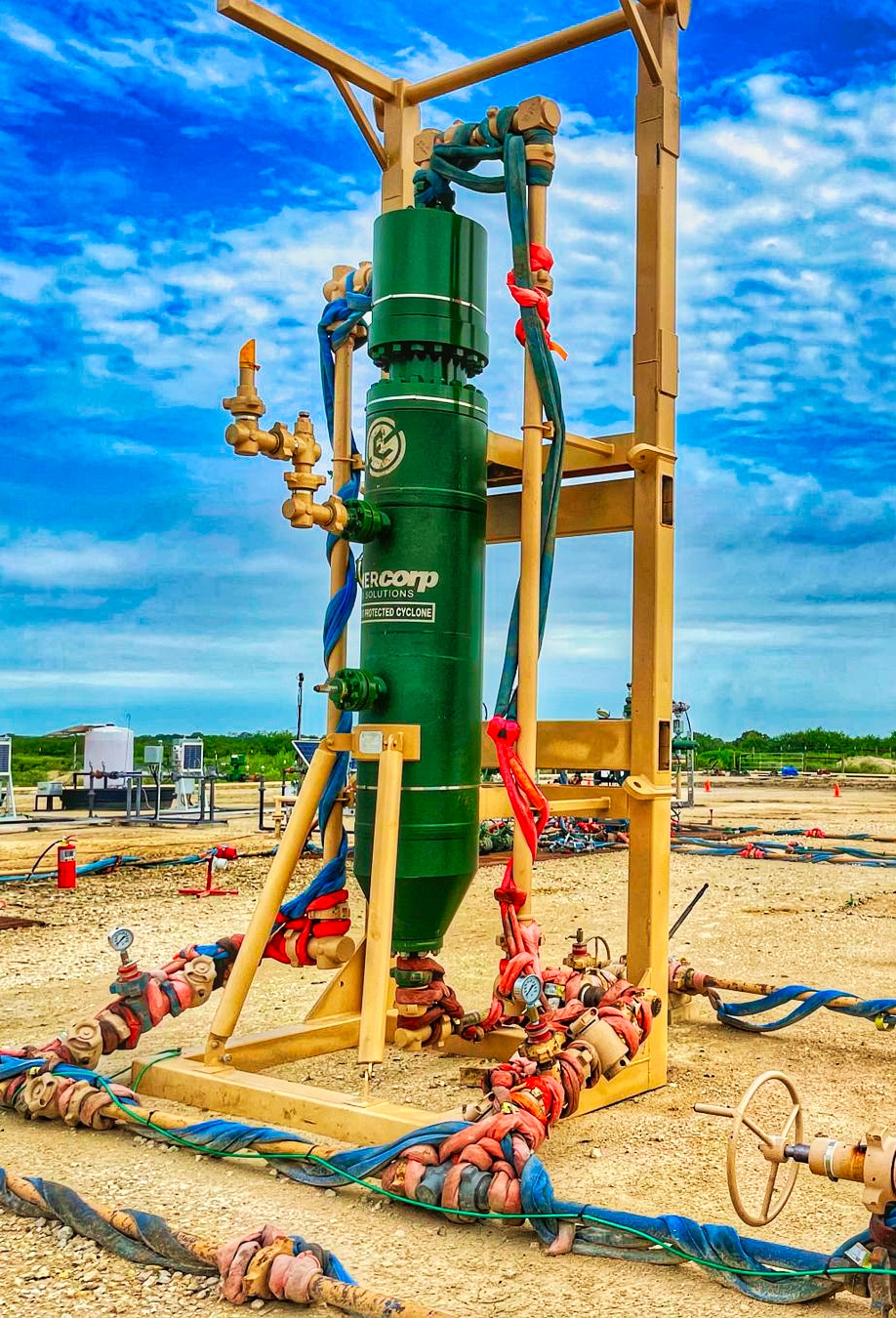