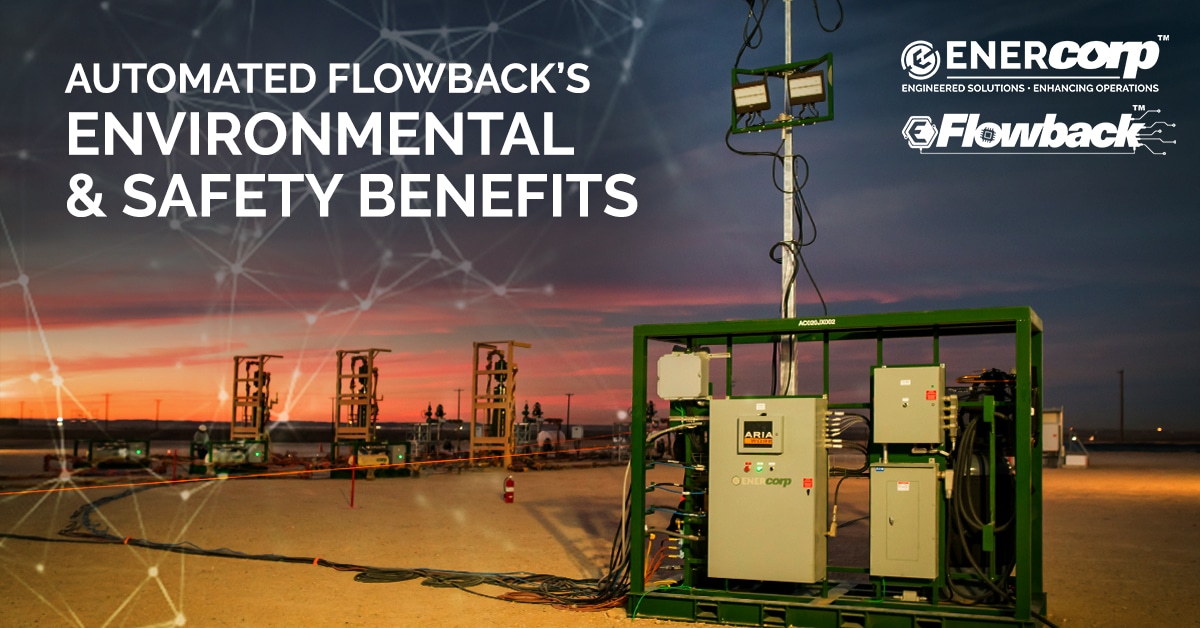
Automated flowback’s environmental and safety benefits (eFlowback)
Estimated reading time: 7 minutes
Table of contents
The status quo of flowback and sand management is changing.
Instead of utilizing commodity equipment that is not fully optimized to clean up the well’s production, operators are looking for highly engineered solutions that can be customized for their specific applications. The traditional approach of hauling out a large amount of equipment to the wellsite, along with a lot of personnel, is obviously very inefficient, but it’s also not environmentally optimized and leads to increased safety risk for personnel.
As the industry leader in sand management services for flowback, EnerCorp offers our clients valuable expertise in optimizing their operations and enhancing production. With the right equipment for the job, our clients can send clean production to their facilities while minimizing their equipment footprint, personnel costs, and HSE exposure.
Flowback 2.0 has truly transformed flowback in the oil and gas industry, particularly in the Permian, Haynesville, Northeast, Eagle Ford, Duvernay, and Montney areas. However, we’re taking things a step further with our newly launched eFlowback technology, which makes automated flowback and sand management a reality in these demanding applications.
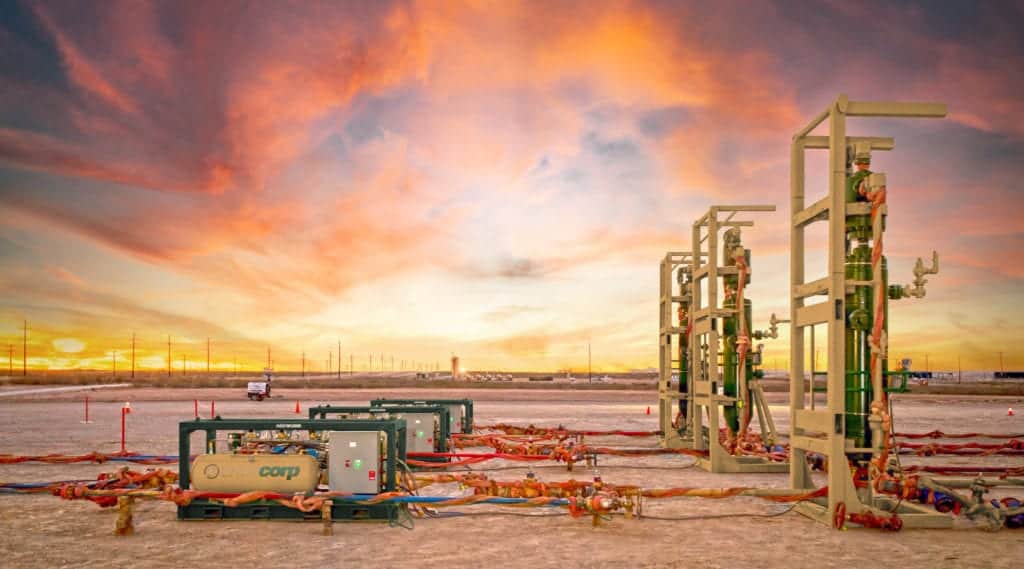
While eFlowback enables operators to reduce their operating costs, we understand that profitability isn’t the only measure of success. Investors, employees, partners, and customers want to know how organizations are improving their environmental, social, and governance metrics — and eFlowback is the answer.
Flowback built with environmental and safety advantages in mind
eFlowback was developed in collaboration with bpx energy, who were instrumental in the system requirements, prototype field trials, and thorough risk assessment. Chris Walker, Facilities Engineer at bpx energy says, “The launch of eFlowback is a major milestone in our industry, enabling us to achieve our safety, environmental, and efficiency objectives. As a result of the early success we have achieved together on this project, bpx energy made a strategic commitment through the end of 2022 to utilize EnerCorp’s eFlowback technology.”
“Their focus on reducing safety risks by minimizing human exposure during the flowback process drove our team to ensure risks were engineered out from becoming significant process control concerns,” explains James Pung, CEO at EnerCorp. “In addition to safety, we were focused on reducing emissions by minimizing truck traffic and monitoring site operating parameters and equipment conditions with cloud-based technology.”
Desanding services for automated flowback
eFlowback brings together EnerCorp’s industry-leading sand management technology with automation, measurement systems, and cloud-based software, enabling operators to autonomously control their flowback operations remotely. With cost reductions that come with digital transformation and workforce optimization, operators also get added environmental and safety benefits.
eFlowback is an entire digital flowback ecosystem, generating great value not from point solutions, but from each piece of technology working together efficiently. Here’s how eFlowback offers operators environmental and safety benefits.
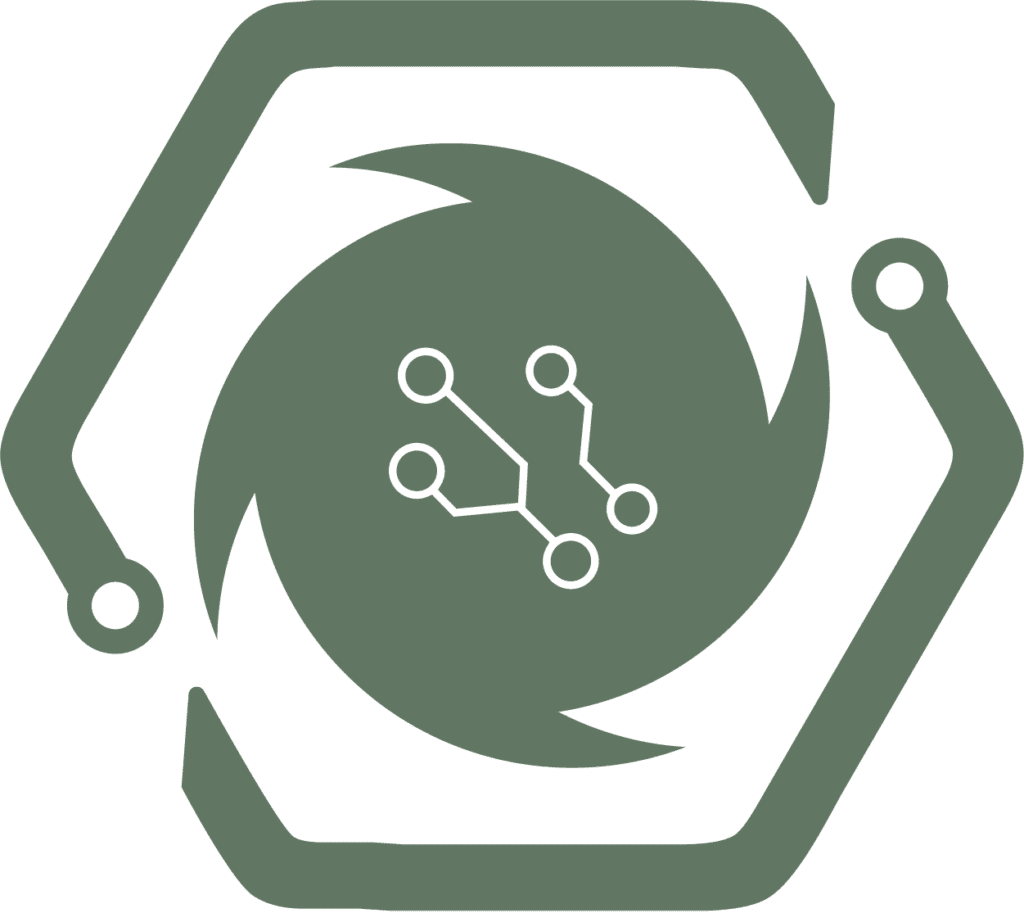
Sahara Advanced Cyclone
The Sahara Advanced Cyclone, which is the market-leading sand separator clients trust, has been precisely engineered to deliver >97% sand capture efficiency across a broad range of flow regimes. This versatile desanding technology reduces the equipment footprint on location while delivering best-in-class sand removal rates. With less desanding equipment on site, there are fewer transportation emissions released into the environment, as well as less trash generated from the minimal personnel required onsite.
By using the Sahara during flowback, operators can bypass frac tanks and flow directly into the production facility and pipelines, as there is no risk of damage from sand particles. This reduces water and oil collection truck traffic, minimizing transportation emissions. Because the sand-free hydrocarbons flow directly into the production facility, the gas does not need to be flared, minimizing emissions even further. Water and oil are no longer stored in frac tanks, eliminating any entrained methane gas being emitted into the environment. Vapor recovery units on storage tanks can recapture any emitted methane as the hydrocarbons flow into the production facilities.
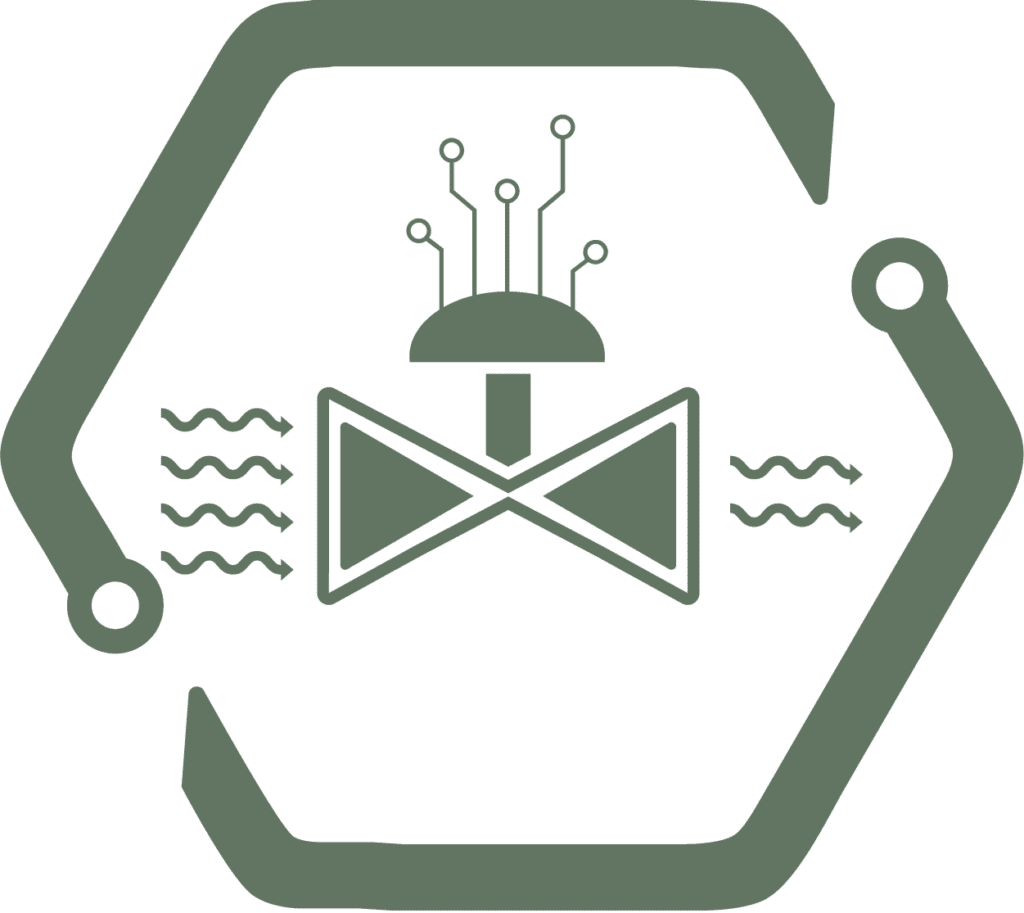
Automated Choke Manifold
Instead of manually performing the choke changes based on a choke schedule, operators can autonomously follow the choke schedule and make real-time adjustments if deviations are needed — all conducted remotely. This means less personnel required on site, as well as lowering transportation traffic and emissions.
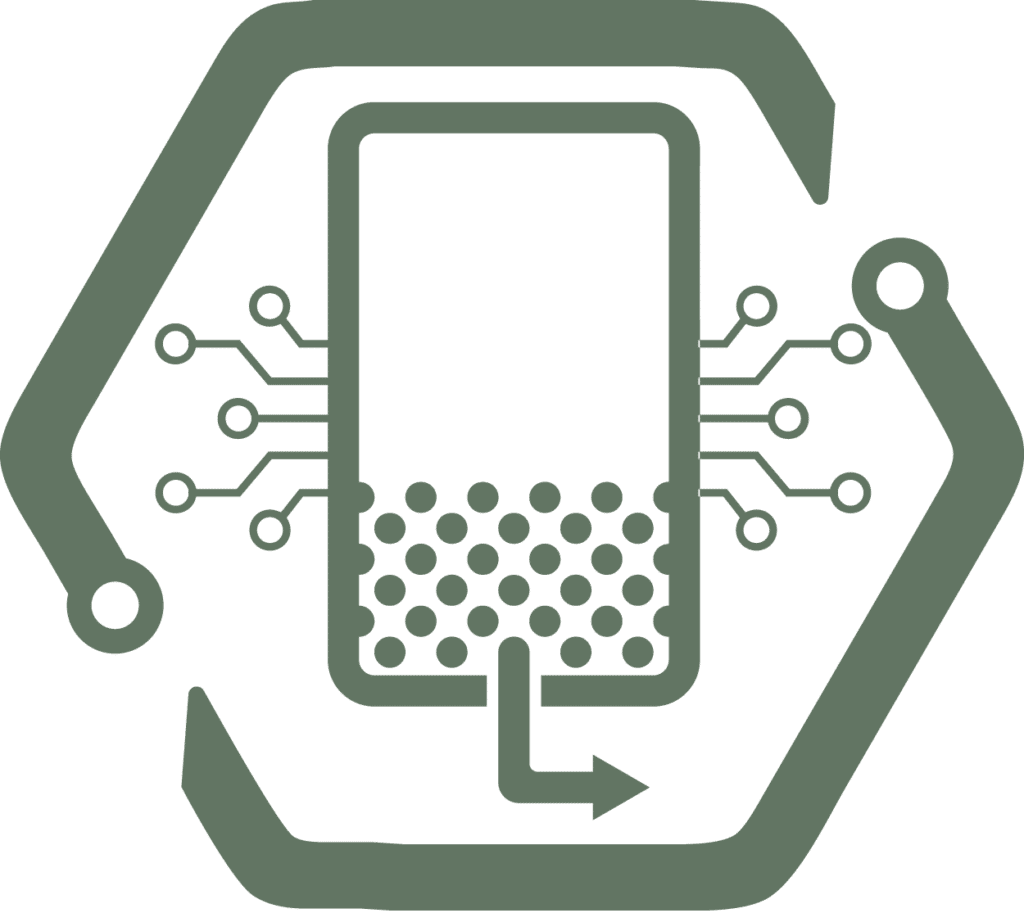
Automated Blowdown Unit
The Automated Blowdown Unit dumps sand from the cyclone and features multiple backup valves to ensure isolation. There is a patent-pending leak detection system, which minimizes environmental exposure as well as personnel safety risks. Operators can remotely detect washed out or stuck valves, sending personnel to fix them before a harmful environmental release occurs.
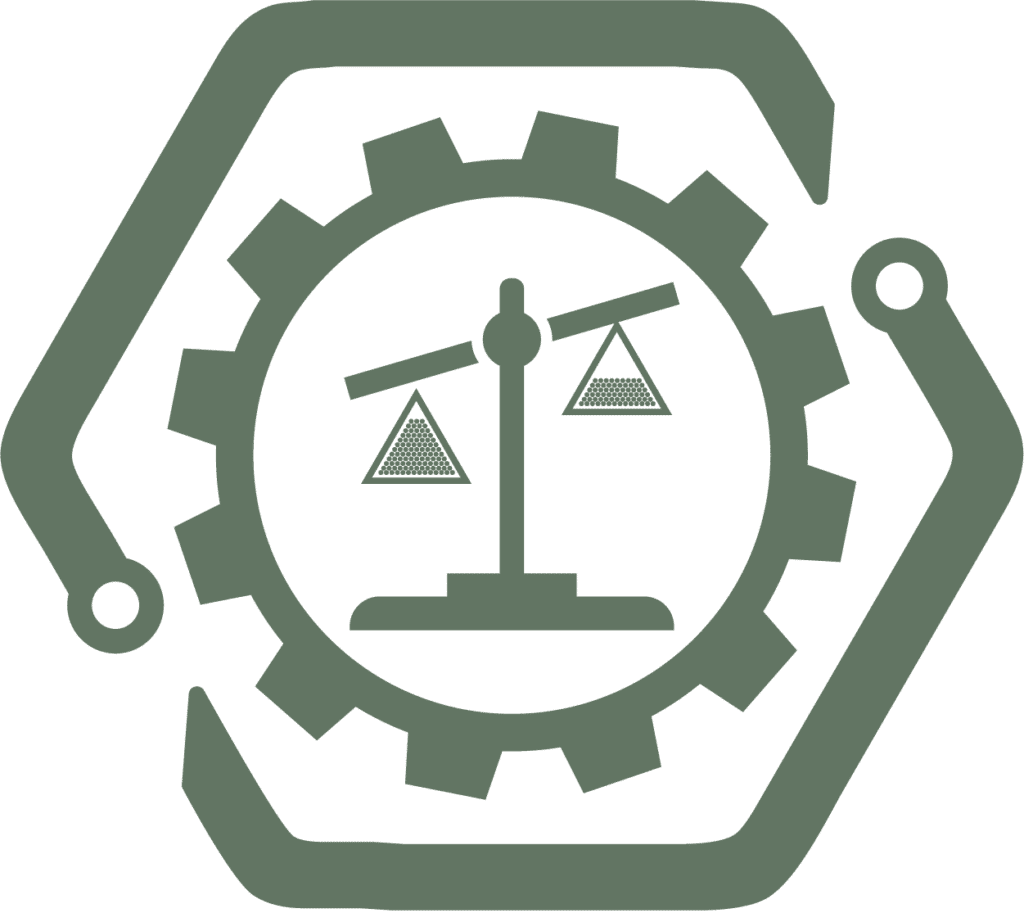
Sand Quantification Unit
There are numerous safety benefits operators can gain when they use the Sand Quantification Unit during eFlowback. Instead of having to manually measure the sand, risking injuries to personnel, operators can track precise weights remotely and see how much sand is produced in each blowdown.
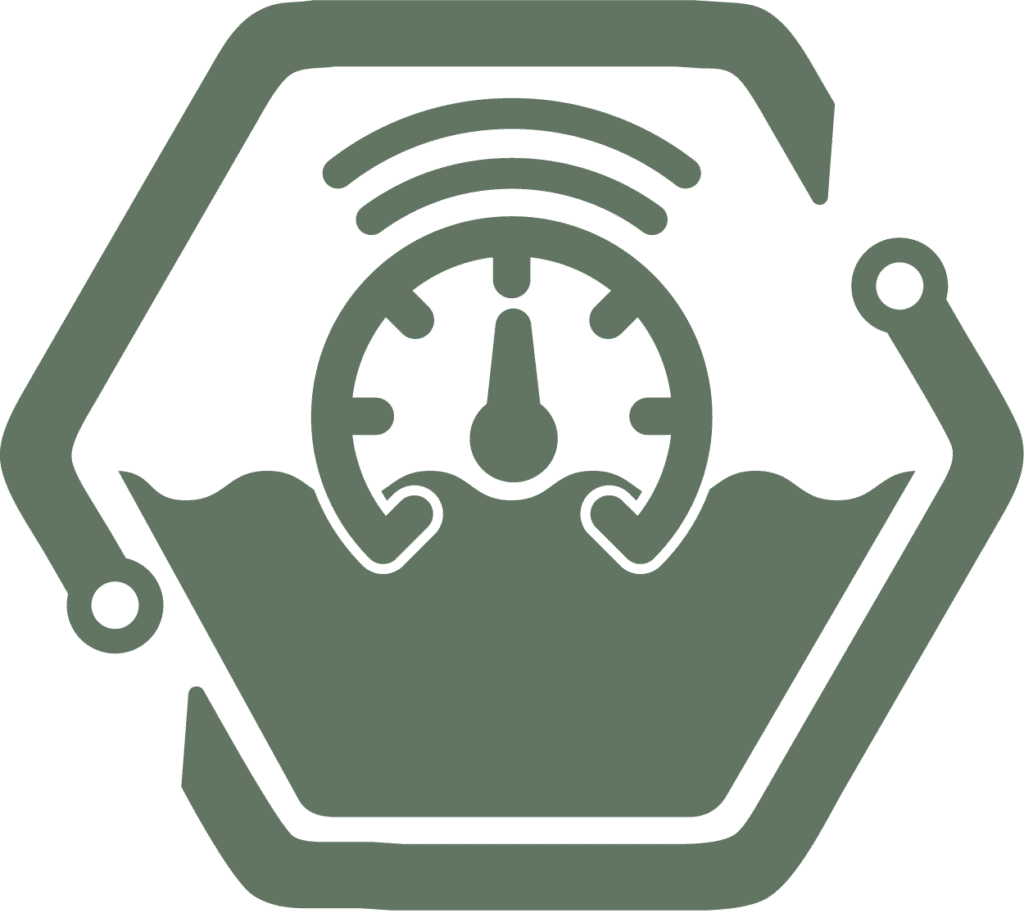
Tank Level Monitoring System
Having multiple checks and balances is key when it comes to environmental and personnel safety. The Sand Quantification Unit, which is connected to the Tank Level Monitoring System, uses laser-level detection to measure the level of fluids with high accuracy. Remotely monitoring the levels, operators receive system alerts when it is time to call a vacuum truck to empty the tank.
The monitoring system can automatically shut down the blowdown unit if it reaches a specified threshold to prevent any harmful releases. In addition, the Emergency Shut Down (ESD) can be configured to communicate with the Tank Level Monitoring System to shut in the well if necessary to completely eliminate any chance of environmental releases during flowback.
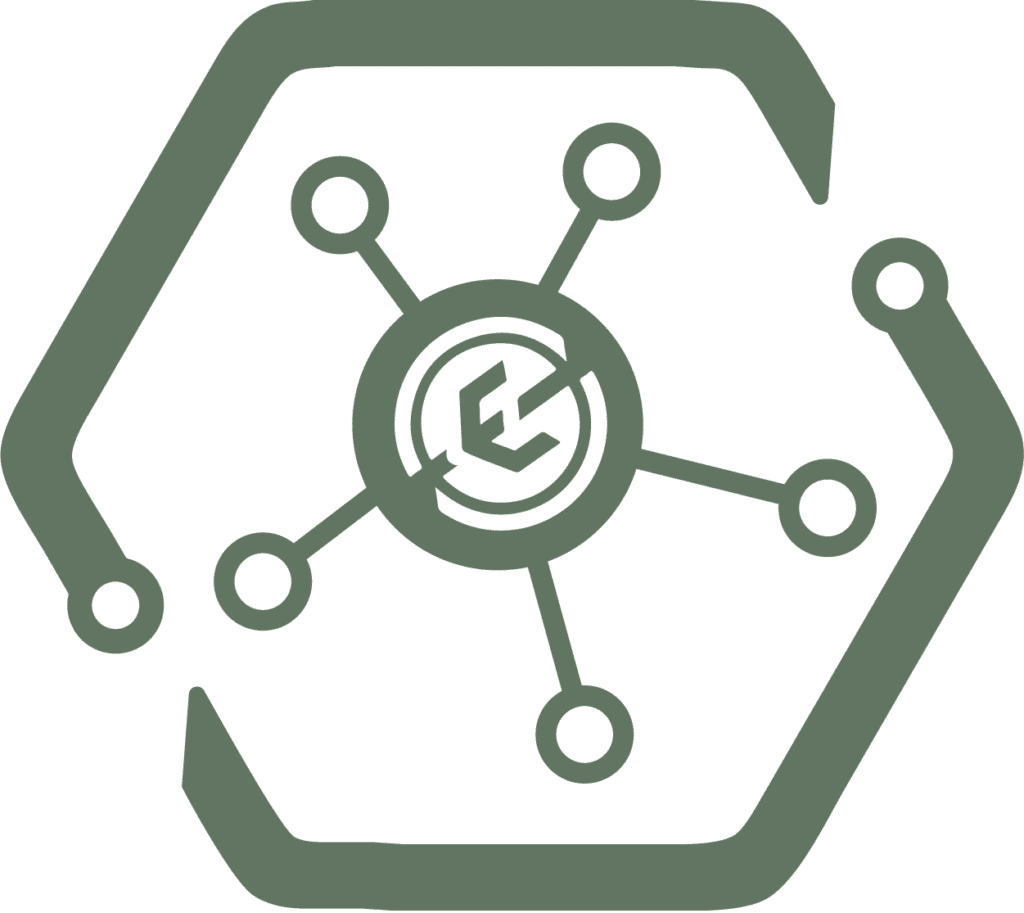
Automated Control Unit
Each piece of equipment in the eFlowback ecosystem is connected to the Automated Control Unit, which is the brain and heart of the technology. It distributes power and air in order for the technology to operate, and provides operators with remote control and visibility into their machines.
The Automated Control Unit has an intuitive graphical user interface so that personnel on site or remotely can access, control, review, and track analytics, and troubleshoot any issues. It also enables personnel to see the status of any device at any time — from any location.
The Automated Control Unit can also be tied-in to your SCADA platform, allowing full system integration, communication, and monitoring in the native environment you are accustomed to.
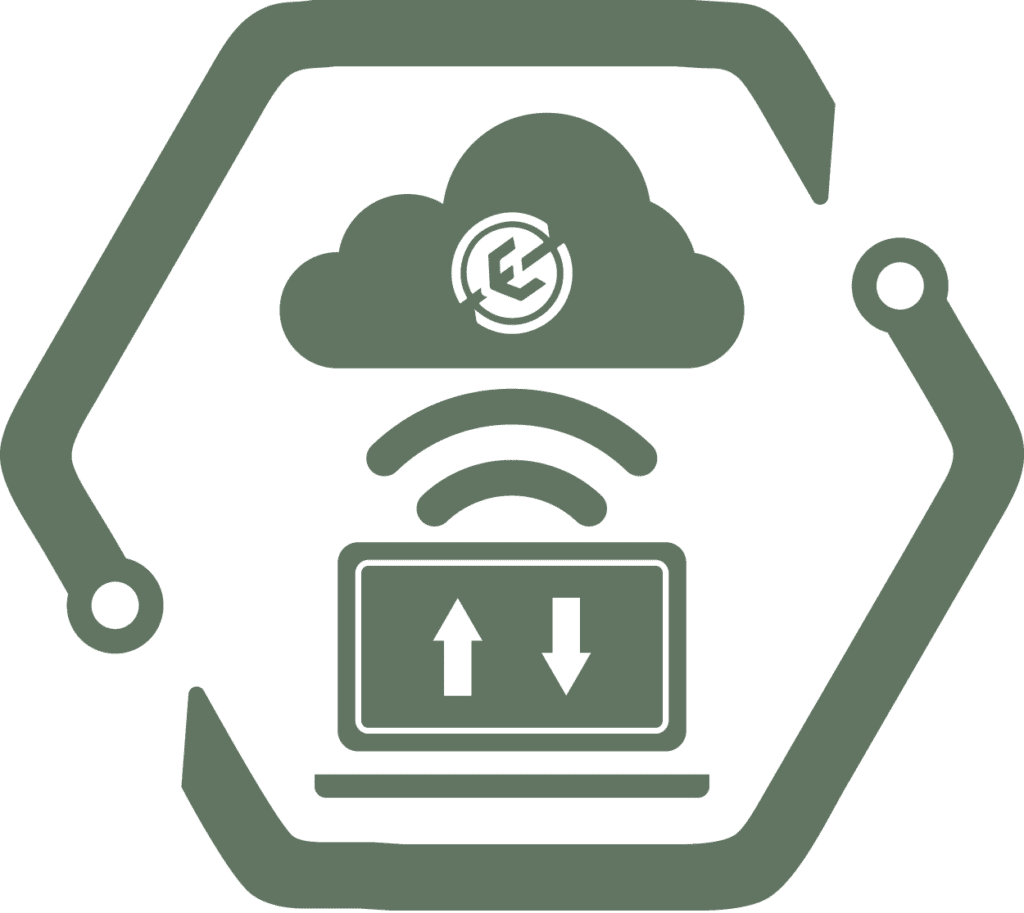
Cloud-Based Software
Safety isn’t just about keeping personnel safe, it’s about keeping the entire company safe. eFlowback runs on highly secure cloud-based software with entitlements based on role, so only the appropriate team members can monitor, review, or control the equipment on site. If an alarm is triggered by any of the technology, the appropriate personnel are alerted so they can take the necessary action right away to minimize environmental and safety issues.
EnerCorp’s highly engineered technology and secure software ensures the operators can manage their flowback remotely. Personnel don’t need to be on site at all times and are only called when they are alerted or required. This results in reduced transport emissions and trash generation overall.
It’s time to make a positive difference to your environmental and safety record
Share this Article