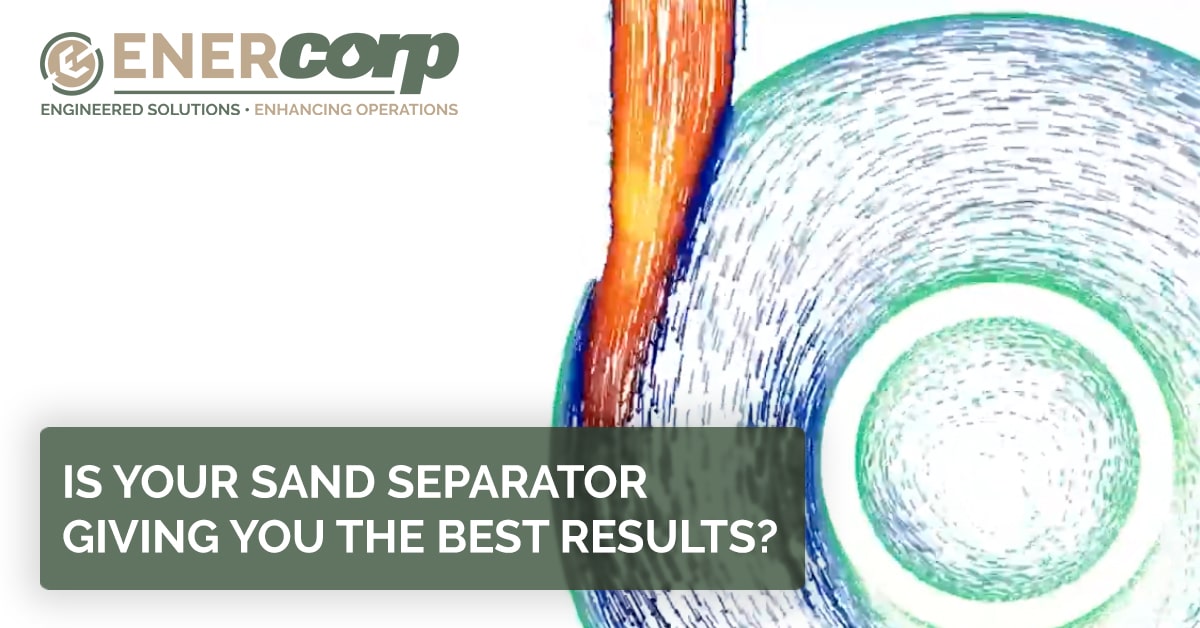
Is your sand separator giving you the best results?
There are a lot of different sand separating technologies on the market, but not all sand separators are created equal.
You may be tempted to go with a less costly sand trap or single-stage cyclone to reduce your operating expenses — but buyer beware!
Just because the sand can or sand knock-out costs less, doesn’t mean you will end up paying less in the long run. You will likely need to use multiple units and you still may not get the sand separation results you need to keep downstream equipment and your production facilities damage-free.
Sand separator, spherical sand trap, desander — which one is right for you?
In your research, you’ve probably come across a number of different sand separation technologies on the market:
- Sand trap for oil and gas
- Sand knock-out
- Sand can
- Spherical sand trap
- Wellhead desander
- Cyclonic sand separator
- Hydrocyclone
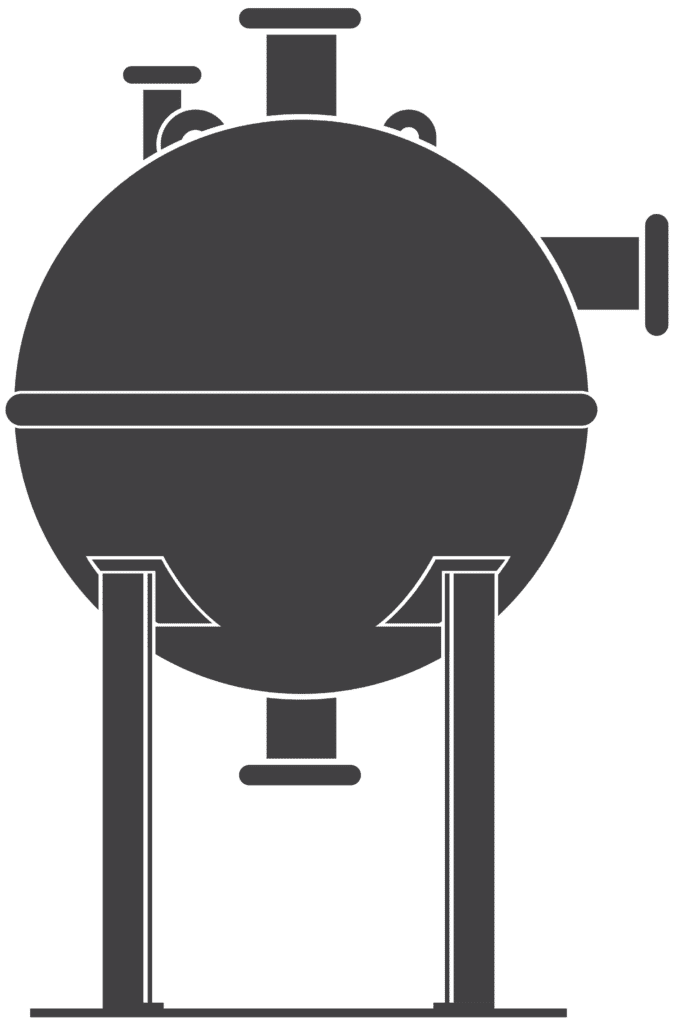
Non-Engineered Sand Separators
On the surface, it seems like all of these technologies do the same thing — separate sand from water, oil, and gas. Some use gravity while others use a cyclonic force, but the goal is the same.
However, it’s important to note that not all sand separating technology will get you the same results.
Many of these options are not properly engineered for sand separation. This means that they are engineered pressure vessels that meet API or ASME standards and codes. They are safe to use on your wellsite in terms of pressure containment. However, the manufacturers typically don’t have engineers on staff that understand the physics of fluid dynamics and separation. Therefore, there is nobody at these companies performing calculations and modeling to optimize the technology and deliver custom solutions based on flow regimes, sand particle size, and other variables.
There is very little research and development, and almost no customization, available on most sand separator products. As a result, you will likely only achieve between 50% and 65% efficiency using one of these units in moderate-to-challenging sand production applications.
In order to achieve the sand separation levels you need to ensure there is minimal damage to your production facilities — which is frequently over 95% — you will need to use multiple units. This means higher operating costs, larger equipment footprint, higher HSE exposure, and increased labor costs.
Sand management services with engineered solutions
EnerCorp specializes in sand management services for flowback and production operations. We have a team of in-house engineers and a research and development department whose sole focus is on optimizing our technology to ensure our clients see the best possible results.
EnerCorp’s engineered sand cyclone technology in our Sahara Advanced Cyclone uses centrifugal force to separate sand from the production stream, providing our clients with over 97% sand capture efficiency. Compare that to the 50% efficiency you frequently see on non-engineered solutions.
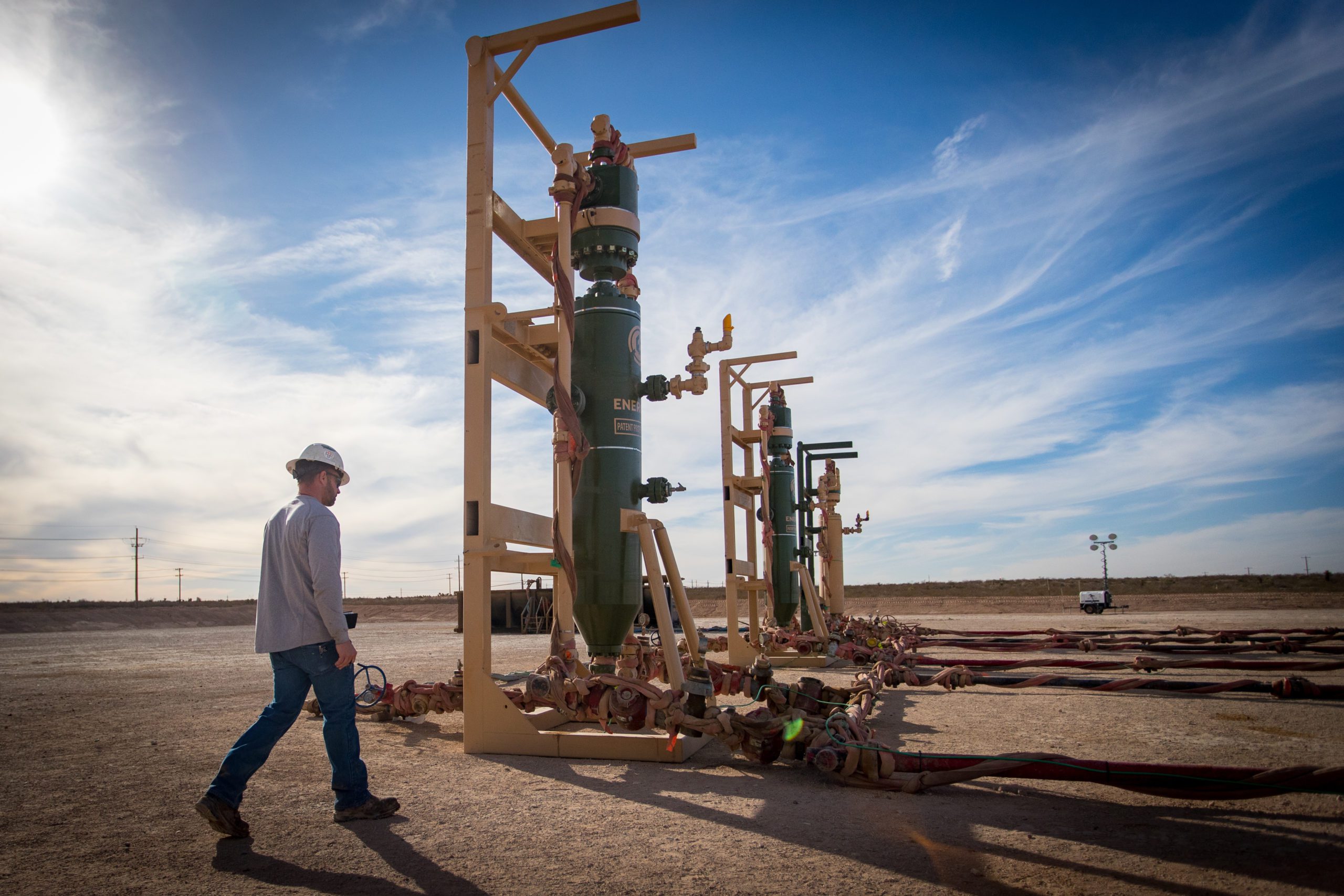
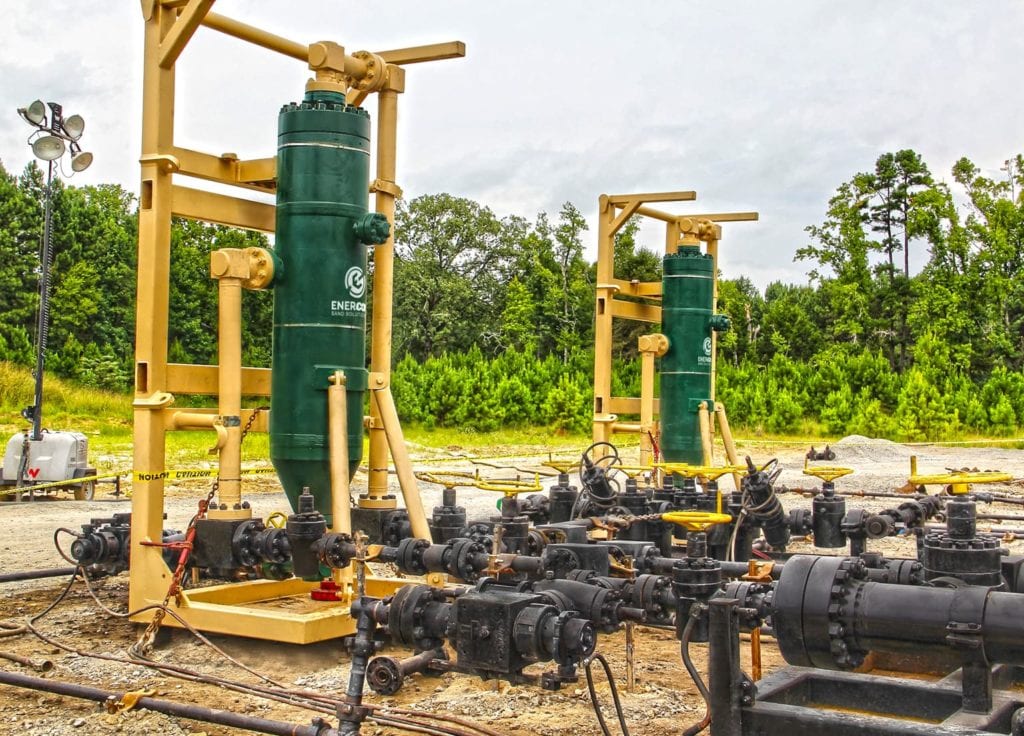
Smaller equipment footprint
Lower operating costs
- Less HSE exposure
- Reduced labor costs
- Minimized environmental impact

50%

75%

88%

94%
CYCLONE

65%

88%

95%

80%

96%

97%
The cyclonic separator that outperforms them all
How did EnerCorp’s hydrocyclone technology reach this level of sand separation efficiency? It’s all in the engineering and development of this industry-leading technology.
When we set out to create the Sahara Advanced Cyclone, our objective was to develop a modular cyclone that delivered over 97% sand capture efficiency for 100 micron and larger particles. This had never been done before by a cyclone designed for our target markets — but our engineers had a process they were confident in.
We followed a multi-variant optimization process utilizing computational fluid dynamics (CFD) to guide all of our design selections. When executing the evaluation process, we considered a broad range of operational and product design characteristics. Variables altered as part of this analysis included:
- Operating conditions
- Range of flow rates
- Varying wellhead pressures
- Various solids / sand particle sizes
- Product design considerations
- Cost
- Inlet size and geometry
- Outlet size
- Cone diameter and height
- Downpipe diameter and height
- Various wall geometries

In addition to our computational modeling, we combined our years of practical experience in the field to develop the Sahara Advanced Cyclone. Our team has worked on sand management projects on thousands of wellsites, and has a great empirically based catalogue of information to reference.
The results of this in-depth engineering and R&D showed us that we can optimize capture rate for even small sand particle sizes across a broad range of well flow conditions by optimizing inlet velocities. This process also led us to design an adjustable inlet so that target inlet velocities can be achieved for a range of flow conditions — which will optimize the vortex created by the cyclone for separation. As such, performing application engineering and product customization before the job starts allows the Sahara Advanced Cyclone to deliver an excellent capture rate regardless of flow rates and pressures.
Sand Separator FAQ
Ready to find a cyclonic sand separator to enhance your flowback and production operations?
Don’t want to waste your time on sand traps and sand cans anymore? We hear you.
Learn more about our industry-leading technology and see how state-of-the-art sand cyclonic separators can enhance your flowback operations, lower your equipment footprint, and reduce your operating expenses — all while removing more sand from your hydrocarbon production stream.
Share this Article